The main production methods of steel pipes
The main production methods of steel pipes
The main production methods of steel pipes are Hot rolled(including extrusion), Welded and cold working. Cold working (Cold rolled, cold drawn and cold spinned) is the secondary processing of steel pipes.
Hot rolled seamless steel pipe
The production process of hot-rolled seamless steel pipe is to perforate and roll a solid pipe blank (or steel ingot) into a steel pipe with the required shape, size and performance. There are three main deformation processes in the whole process: 1) perforation—through solid billets (ingots) into hollow capillary tubes; 2) pipe rolling—rolling capillary tubes into rough tubes close to required size; Barren pipes are rolled without core rods into finished pipes with the required dimensional accuracy and trueness. In production, different types of pipe rolling mills are selected according to different conditions such as product variety, specifications and production capacity. Because different types of pipe rolling mills have different kinematic conditions, stress conditions, pass deformations, total deformations, and productivity, they must be equipped with a matching amount of deformation and productivity. Punchers and other equipment for the front and rear processes. In this way, different tube rolling mills constitute different tube rolling mills. The production methods of hot-rolled seamless steel tubes are classified according to the type of tube rolling mill in the unit. The current common production methods of hot-rolled seamless steel tubes are shown in Table 1. The specific name of a unit is expressed by the type and specifications of the unit and the type of pipe rolling mill. For example, the 168 continuous pipe rolling unit refers to a unit whose maximum outer diameter is about 168 mm and the pipe rolling mill is a continuous pipe rolling mill. The maximum technical pressure (tonnage) of the extruder or the range of product specifications is used to indicate the model of the steel tube hot extrusion unit.
Production method | Raw material (tube blank) | Equipment for main deformation processes | Product Range | ||||
Perforation | Rolled tube |
Outer diameter(OD) (mm) |
Wall thickness(WT) (mm) |
OD/WT | Maximum length of waste pipe(m) | ||
Automatic tube rolling unit | Round billet |
Two-roller oblique rolling perforator Barrel roller or tapered roller |
plug mill | 12.7~426 | 2~60 | 6~48 | 10~16 |
Continuous casting round billet | |||||||
Continuous casting billet | Pushing and Punching Machine (PPM) and Stretcher | 165~406 | 5.5~40 | ||||
Continuous rolling mill |
Round billet |
Two-roller oblique rolling perforator Barrel roller or tapered roller |
MPM, PQF | 16~194 | 1.75~25.4 | 6~30 |
20~33 |
Continuous casting round billet | |||||||
Continuous casting billet | Pushing and Punching Machine (PPM) and Stretcher | MPM | 48~426 | 3~40 | 6~40 | ||
Three-roller tube rolling unit |
Round billet Continuous casting slab |
Two-roll diagonal or three-roll diagonal | ASSEL | 21~250 | 2~50 | 4~40 | 8~13.5 |
Pilger rolling mill | Round ingot | Two-roll oblique rolling perforation | Pilger rolling mill | 50~720 | 3~170 | 4~40 | 16~28 |
Square or polygonal ingots | Pressure piercing and diagonal rolling extension | ||||||
Continuous casting tube | |||||||
Pipe jacking unit | Billet | Pressure piercing and diagonal rolling extension | Pipe jacking unit | 17~1200 | 3~220 | 4~30 | 14~16 |
Round billet | Oblique rolling perforation | ||||||
Hot extrusion unit | Round, square or polygonal ingots | Pressure perforation or pressure perforation after drilling | Extruder | 25~1425 | 2~ | 4~25 | ~25 |
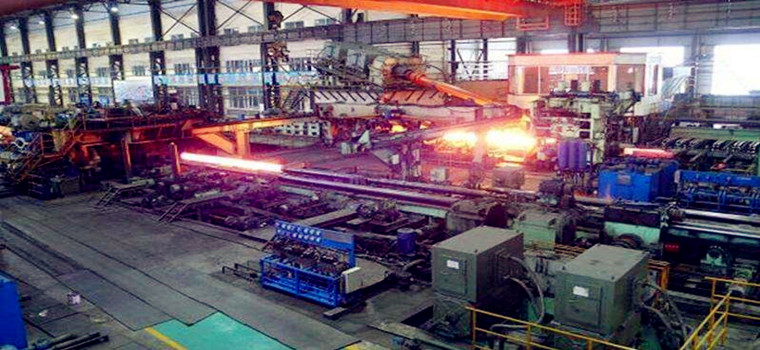
Welded steel pipe
The production method of welded steel pipe is the process of bending the tube blank (steel plate or steel strip) into the required cross-sectional shape by various forming methods, and then welding the seam by different welding methods. Forming and welding are the basic procedures. Welded pipe production methods are classified according to the characteristics of these two procedures. Continuous straight seam welding mainly uses two methods: ERW and high-frequency welding. The UOE method is the main method for producing large-diameter straight seam welding, which is discontinuous. There is also spiral welding, which is mainly used for large-mouth production when the width of the steel plate is restricted The approach taken by the machine.
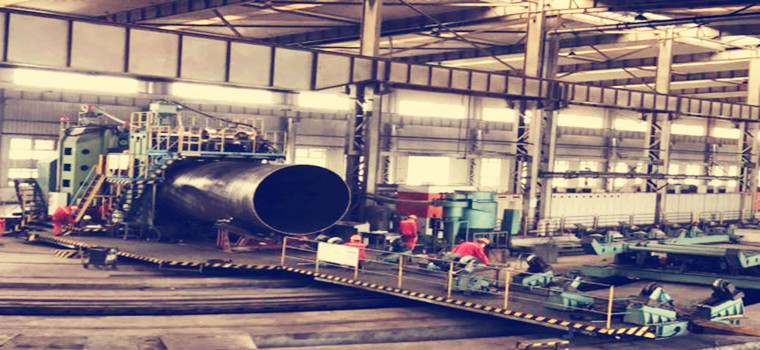
Cold rolled, cold drawn and cold spinned steel pipes
There are three cold working methods for steel tubes: Cold rolled, cold drawn and cold spinned. The product ranges are shown in Table 2. Cold spinning is also essentially cold rolling. The specifications of cold rolling mills and cold spinning machines are expressed by their product specifications and rolling mill models; the specifications of cold drawing machines are expressed by their allowable rated drawing force. For example, LG-150 indicates a two-roller cycle cold-rolled tube mill with a maximum outer diameter of 150 mm; LD-30 indicates a multi-roller cold-rolled tube mill with a maximum outer diameter of 30 mm; LB-100 indicates the drawing force rating. 100-ton cold drawing machine.
Cold working method | Steel pipe Range | ||||
Outer diameter OD(mm) | Wall thickness WT,(mm) | OD/WT | |||
max | min | max | min | ||
Cold rolled, | 500.0 | 4.0 | 60.0 | 0.04 | 60~250 |
cold drawn | 762.0 | 0.1 | 20.0 | 0.01 | 2~2000 |
cold spinned | 4500.0 | 10 | 38.1 | 0.04 | Up to 12000 |
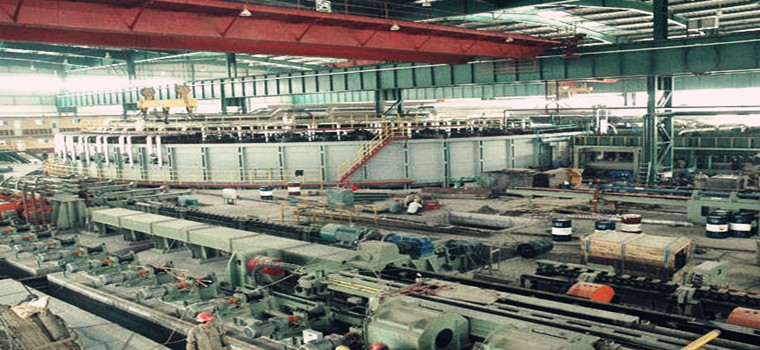